By Victor Tirado, P.E., M.SAME, and Henrik Dahl, M.SAME
At Naval Base San Diego, a complex project to modernize Dry Dock No. 1 required thorough understanding of the facility and careful construction techniques in order to meet current and future demands, and prolong its service life.
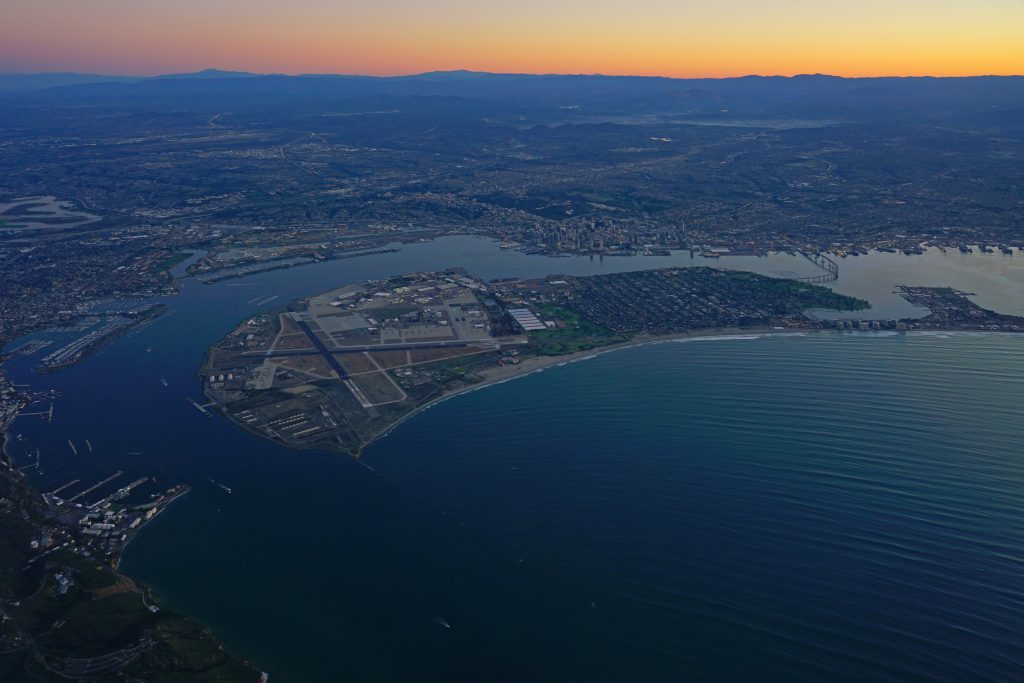
PHOTOS COURTESY GHD
In 1942, during World War II, Dry Dock No. 1 was built at Naval Base San Diego with a configuration to meet the requirements of the naval feet at that time. In the 80 years since, the U.S. Navy has gone through many feet upgrades, while Dry Dock No. 1 has remained largely the same.
Recognizing the limitations to dry dock operations posed by its configuration, the Navy identified several upgrades to modernize the dock to meet current and future demands and prolong its service life, making it among the first dry docks to be modified since the World War II-era. The newly modernized Dry Dock No. 1 is the first of its kind on the Pacific coast and the Navy’s second largest surface ship dry dock overall, spanning 4.8-acres.
A Crucial Need
In 2016, the USS Howard was docked at Naval Base San Diego requiring emergency repairs to its shaft and supporting equipment. Although Dry Dock No. 1 was available, the berth could not accommodate a DDG-51 class vessel because of its sonar dome. This identified an urgent need to provide space for these vessel types.
A joint venture, GHD-COWI JV, worked under contract with the Navy to identify modifications to the dry dock that would allow it to accept DDG-51 class vessels that are equipped with a sonar dome under its keel. The modifications would require repairing a portion of the dry dock floor (and avoid retrofitting the entire dry dock). Other repairs were identified as well, including replacing the dewatering pumps that were beyond their operation life. The contracting team worked closely with the Navy to develop outside-the-box engineering solutions to overcome challenges that could be replicated for other facilities going forward.
System Replacement
The project had four main components, each with its own unique set of challenges: a retrofit design of mechanical systems; dredge design for the access channel and turning basin; construction of a new sonar dome pit on the floor of the dry dock.
Mechanical Systems. Dry docks involve docking a ship into a sealable basin able to be drained so that maintenance can be performed. This requires extensive mechanical systems located in a pump room beside the dock as well as large diameter culverts under the dry dock that reach depths of 60-ft below sea level.
As part of ongoing asset management and maintenance efforts by the Navy, multiple repairs and upkeep procedures have occurred on all pumps. However, no large-scale overhauls on the major pumps had taken place in over 45 years. A recent condition assessment of the motor/pump room determined that the dewatering pumps, drainage pumps, and sump pumps (and their corresponding valves, piping, and appurtenances) were all in poor condition. Beyond their useful lifespan, they required replacement.
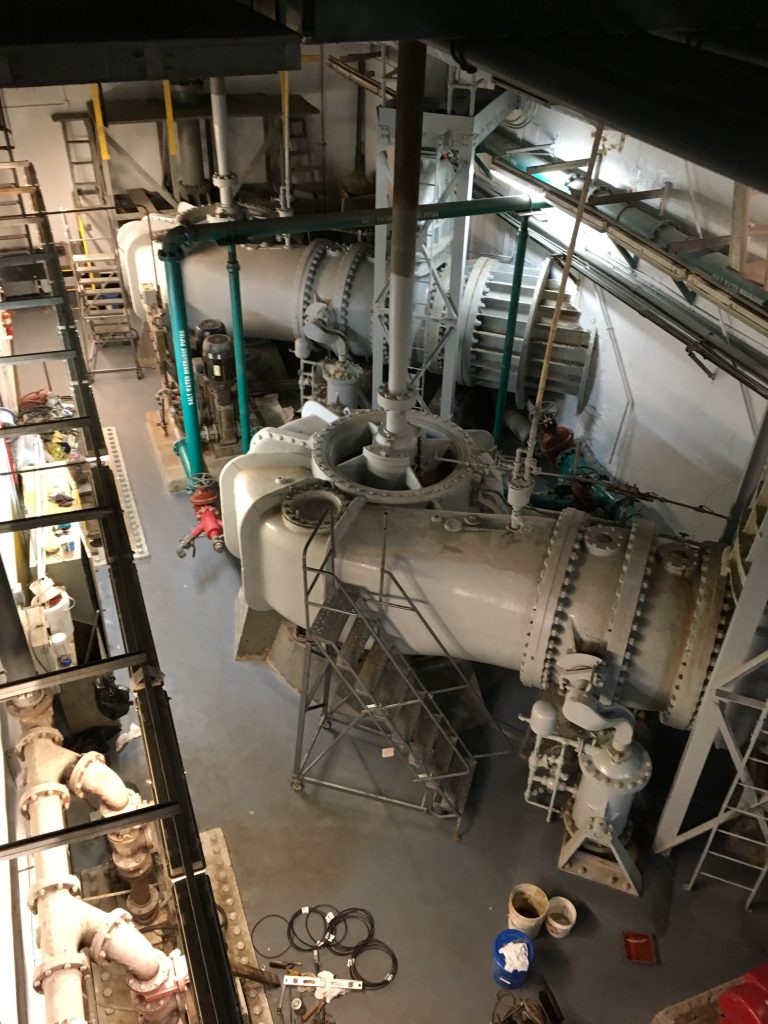
The pumps stand 20-ft tall, with piping systems reaching up to 54-in in diameter. The pumping system for Dry Dock 1 was converted from a pair of 800-hp centrifugal flow pumps to two 800-hp axial flow pumps. Also replaced were two 54-in diameter gate valves, two 150-hp pumps, and two 20-hp pumps.
The modernized technology used on the new pump system works better for low water levels and allows for continuous operation with no need for substitute pumps for when the water levels decrease below the culvert levels under the dry dock. Additionally, the pump upgrades required operational system upgrades to the dry dock computer systems and controls.
The design team performed a complete evaluation of the hydraulic and electrical systems, as well as assessed the structural integrity of the existing motor/pump room. A complete inventory of the facility determined the extent of the replacement work to take place, along with evaluating the ability to install newer, more capable systems using the same configuration.
The team performed market research to locate potential replacement pump manufacturers. These studies revealed that the existing facility could accommodate new pumps and ancillary equipment using the same configuration. However, it also highlighted that the pumps needed to generate the necessary flows to dewater the entire dry dock in less than two hours were no longer manufactured in the United States. The team worked closely with manufactures to develop performance specifications that would allow existing domestic manufacturers to custom build the required 800-hp axial flow pumps.
Sonar Pit Dome. As demonstrated during what occurred with the USS Howard, the dry dock required a sonar dome pit so that DDG-51 class vessels could be accommodated. This portion of the project was uniquely challenging. The concrete floor had to be cut at 40-f below sea level, but water pressures would cause the floor to be forced up or geysers to be formed unless a more innovative approach emerged.
The stability of the dry dock was accomplished by using mass concrete that counteracts the uplift pressure of almost 50-ft of water. To avoid lowering the safety factor against uplift, a total of 84 micro piles were installed. These micro piles were anchored into the ground underneath the graving dock, and the tiedown capacity compensated for the ballast of the removed concrete. The team had to lower a portion of the dry dock floor by demolishing portions of existing 15-ft thick concrete flooring, drilling, grouting, and installing the new micro piles. This approach helped achieve significant construction time and cost savings.
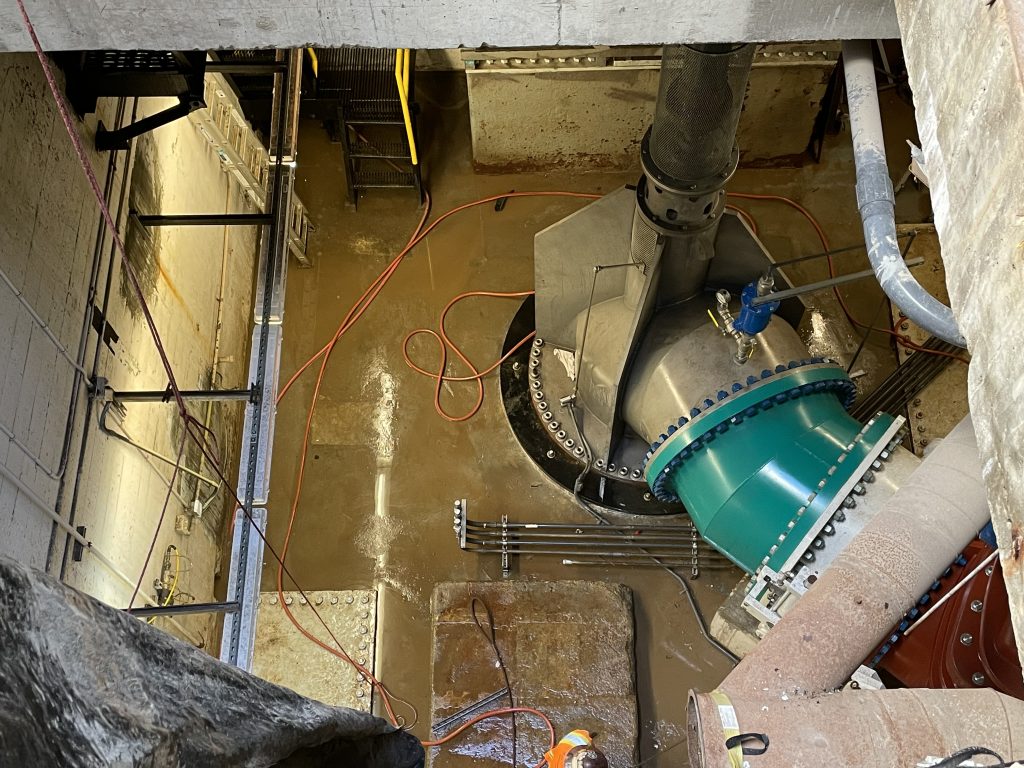
Rail System. A vessel in-haul system is effective in docking a ship into a repair dock, where speed of docking and un-docking is crucial. The previous method of docking the vessels at Dry Dock No. 1 involved using the capstans and manually tying off to bollards as the ship was moving into, or out of, the dock. This procedure required experienced personnel and involved risks.
A trolley-based in-haul system was implemented for more precise horizontal control of the vessels during the docking process. To install it, re-dredging had to be completed on the access channel and turning basin. Consisting of four trolleys (two located close to the bow and two located close to the stern), in-haul rails on both sides of the dry dock, and a capstan at the end of the dry dock to pull the ship, the process of docking the vessel is now much better controlled.
Fleet Operations
Early and thorough understanding of Dry Dock No. 1 being retrofitted was critical for the success of the project. With the upgrades performed to the facility, usage has been extended by decades and been made more reliable.
With aging shipyard infrastructure, it is very important to perform continuous maintenance and upgrades to maintain operational readiness. As the Navy invests in modernizing its shipyards in support of its mission to ensure freedom of the seas, lessons learned from the renovation at Naval Base San Diego can play an important role in long-term stability of fleet operations.
Victor Tirado, P.E., M.SAME, is Maritime & Coastal Market Lead, GHD; victor.tirado@ghd.com.
Henrik Dahl, M.SAME, is Chief Project Manager, COWI North America; hkd@cowi.com.
More News from TME
-
Setting Standards For the Future at Norfolk Naval Shipyard
The renovation for Dry Dock 4 at Norfolk Naval Shipyard, utilized advanced 3D and scale modeling to guide the design choices that would prepare the facility for another 50 years of service while meeting increased standards for resiliency and redundancy. -
Improving NAVFAC’s Facilities Construction Community
Naval Facilities Engineering Systems Command has implemented a series of process improvements across its construction workforce to increase recruitment, validate and standardize mastery of processes and procedures, and recognize accomplishments of personnel. -
Designing and Constructing Secure Spaces at China Lake
As part of the earthquake recovery program at Naval Air Weapons Station China Lake, nearly 300,000-ft2 of secure space must be constructed, requiring an integrated team of government owners, stakeholders, and industry members.