By Rear Adm. Kevin Cook, USCG (Ret.) and Aziz Bamik
The logistics of fuel delivery, storage, and distribution is a critical component to U.S. Navy readiness. Most military logistics demands have a requirement for bulk petroleum products that is significantly larger than other supply classes. Meeting this need requires careful attention at every step to ensure there are no adverse environmental impacts.
A vital aspect to the success of this logistics chain is the performance of fuel storage tanks. While tank designs do follow proven, rigorous standards set by industry and the defense community, special circumstances can arise where innovative solutions may be required. Recently, in order to meet unique environmental and facility requirements, Naval Facilities Engineering & Expeditionary Warfare Center (NAVFAC EXWC), supported by the Defense Innovation Unit (DIU), sought an innovative concept derived from state-of-the-art technology for the storage of liquefied natural gas.
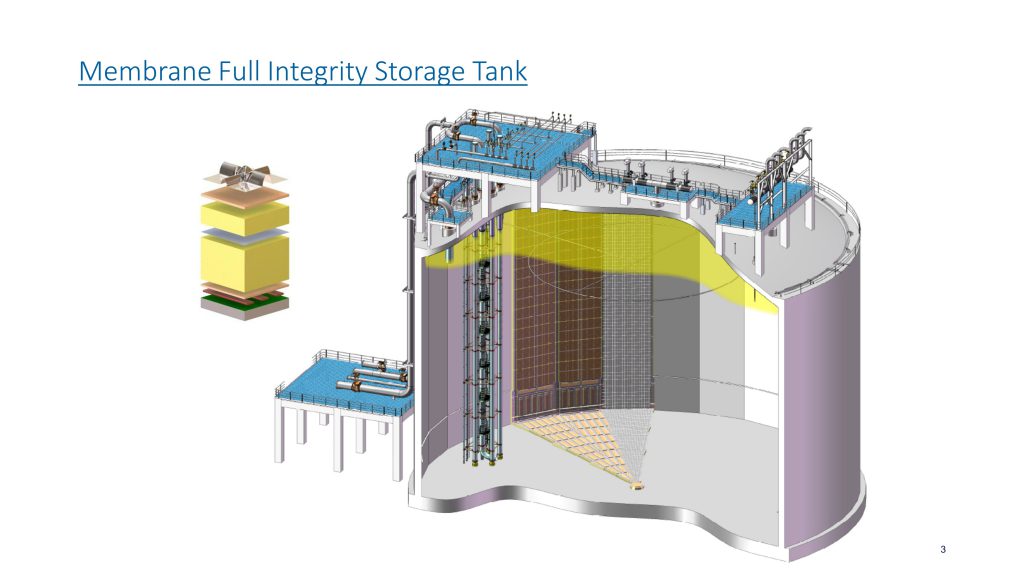
Study and Analysis
In pursuing this solution, DIU began by identifying industry companies with the capability to develop solutions for ensuring bulk fuel storage integrity. The agency sent proposals, and, through a competitive multi- phased process, GTT North America was selected. What set the acquisition apart is that in making the selection, DIU was able to exercise Other Transaction Authority and leverage the flexibility of its experience facilitating a wide range of novel solutions to enable commercial companies to address national security problems.
Stored at -256°-F, liquefied natural gas is well-known for its cryogenic and flammability hazards. The existent tank design had a number of essential capabilities that made it appealing for a fuel storage application. These included a proven double wall for all standard installations; an inherent capability for designs with continuous monitoring for leaks; built-in seismic resiliency; and a modular construction sequence to help overcome tank access and site limitations.
The new design concept was formulated over a period of 20 months, which included a study of the selected facility’s current situation, site visits, engineering and analytical analyses, laboratory testing, and innovative thinking. The work was undergirded by strong collaboration between EXWC and GTT, and the flexibility to advance iterative, progressive solutions through DIU’s contract facilitation.
A dual membrane design was utilized for the fuel storage solution. The primary and secondary metallic liners (typically “barriers” or “membranes”) were designed with a regular pattern of corrugations. These are necessary for the expansion and contraction associated with cryogenic liquified natural gas applications. Innovatively re-purposed, the corrugations provide elasticity to accommodate hydrostatic and seismic load absorption. The interbarrier space, which typically contains insulating material, was also repurposed to allow for the flow of inert gas to sweep for leak detection.
For a fuel tank application, the customary insulation material for the interbarrier spaces was replaced by an inert-to-fuel spacer material that performs a dual function. First, it is porous enough to allow for inert gas to flow through it; this allows for detection of any hydrocarbon leaks. Secondly, it is strong enough to provide the necessary structural support between the primary and secondary membranes.
To further the design concept, and leveraging experience from other tank applications, the intention was for components to be pre-assembled into sandwich-style panels, including all but the primary metallic membrane (to be welded on the face of panels later). Panels would be manufactured in sizes to accommodate limited tank access dimensions and installed by attaching the panel to the existing tank wall. The sandwich panels require pre-welded studs on the existing tank wall at very precise locations to accommodate their fixture. Additionally, the panels also must have a perfectly flat surface at their back to ensure alignment and continuity of the membranes and interbarrier space. This is the process minimally modified to retrofit an existing tank while improving environmental performance.
After careful analysis, a grouting method was selected to provide the most versatile solution to address different surface conditions within each tank and from tank to tank. Exactingly pumping grout behind the panels was determined to be the best process. A total of three families of grout (mortars, resins, and polyurethane foams) in 15 different formulations were evaluated before the final selection was made. This process provided a very versatile solution and a reliable way to address any unique application in the future.
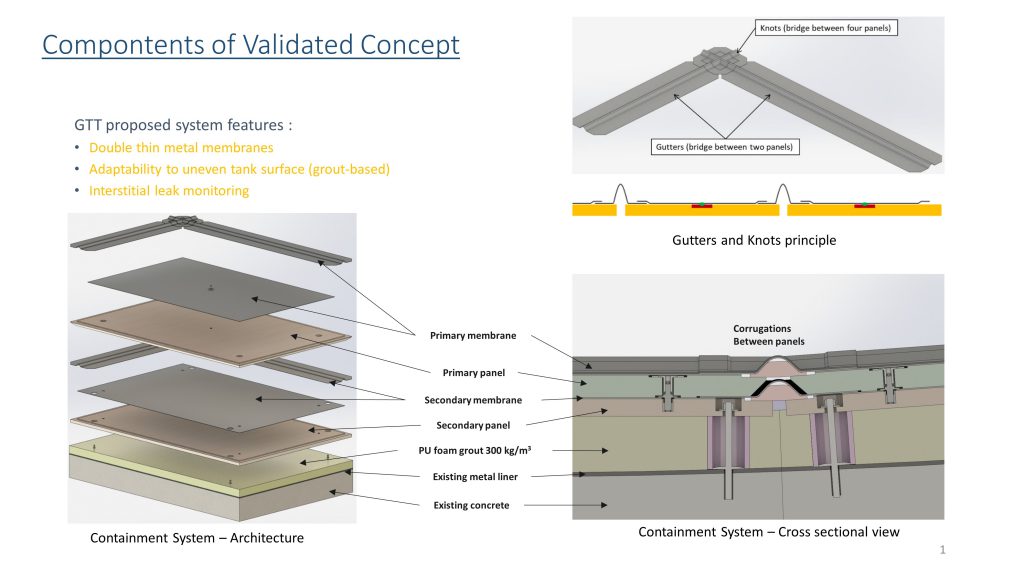
Membrane Selection
Another area of significant engineering study was the compatibility of materials in the sandwich panel, especially the primary membrane that would be in contact with the fuel oil. When used for liquified natural gas applications, the primary membrane is typically made of 304L stainless steel. Moreover, the metal selected for the primary membrane had to be resilient to the potential presence of harmful anions, since the solution is expected to be in-service for the lifetime of the tank without maintenance. Compatibility with all typical fuel contaminants required extensive laboratory testing. This would not have been possible without extensive coordination with facility operators.
There were nine candidate metals considered for the primary membrane. They were tested on their weldability, formability, fuel compatibility, electrochemical resistance, and coating compatibility. After nearly 700 immersion and mechanical tests, conducted both in laboratory and in situ, Inconel 625 was the preferred option.
Logistical Benefits
While a host of technical issues were addressed in the concept review, the surface leveling (grouting) and primary membrane metal selection were presented as illustrative of the comprehensive nature of work conducted. It also portends the degree of understanding that could be generated to apply to other unique fuel tank applications, including both new construction and retrofits. Although not developed more, the concept additionally provides a number of logistics benefits where physical limitations affect the tank or the surrounding site access.
In view of a tightening environmental compliance throughout the world, the concept embodies significant advantages. Chief among these is the metal double wall and the continuous leak monitoring in the interbarrier space. Preliminary technical feasibility was successfully demonstrated at an existing fuel facility. While the project ended before the concept could be prototyped, there are 60 years of experience behind the design being applied in liquified natural gas storage and transportation—providing high confidence in its environmental performance.
The concept is further applicable to several classes of asset management challenges, including environmental security, tank retrofits, modular construction, and seismic resiliency.
Rear Adm. Kevin Cook, USCG (Ret.), is Executive Advisor, and Aziz Bamik is General Manager, GTT North America. They can be reached at kcook.ext@gtt-na.com; and abamik@gtt-na.com.
More News from TME
-
Assessing Mobile Nuclear Reactor Usage in the Pacific
A research team at the Air Force Institute of Technology carried out a lifecycle assessment of the environmental impacts, operational viability, and logistical considerations of mobile nuclear reactors in the Indo-Pacific. -
Embracing Modern Mass Communications Systems
Modern mass communication systems utilizing Internet Protocol-based adoption offer many benefits over legacy analog systems for military bases, including critical issues of security, functionality, and compliance to meet evolving expectations, standards, and safety requirements. -
Developing a Maglev Network for National Defense
A transportation network leveraging superconducting magnetic levitation technologies would bring benefits for logistics, surface transportation, and energy storage, as well as strengthen national defense priorities and the defense industrial base.