Design and Construction
By James Bush, P.E., M.SAME, Daniel Olivas, P.E., PMP, Jerry Nicholson, and Bill Nieport, RA, PMP, LEED AP, M.SAME
To construct a 76,000-ft2 state-of-the-art aquatic training center at Joint Base San Antonio-Lackland required overcoming various technical complexities and extensive teamwork between stakeholders.
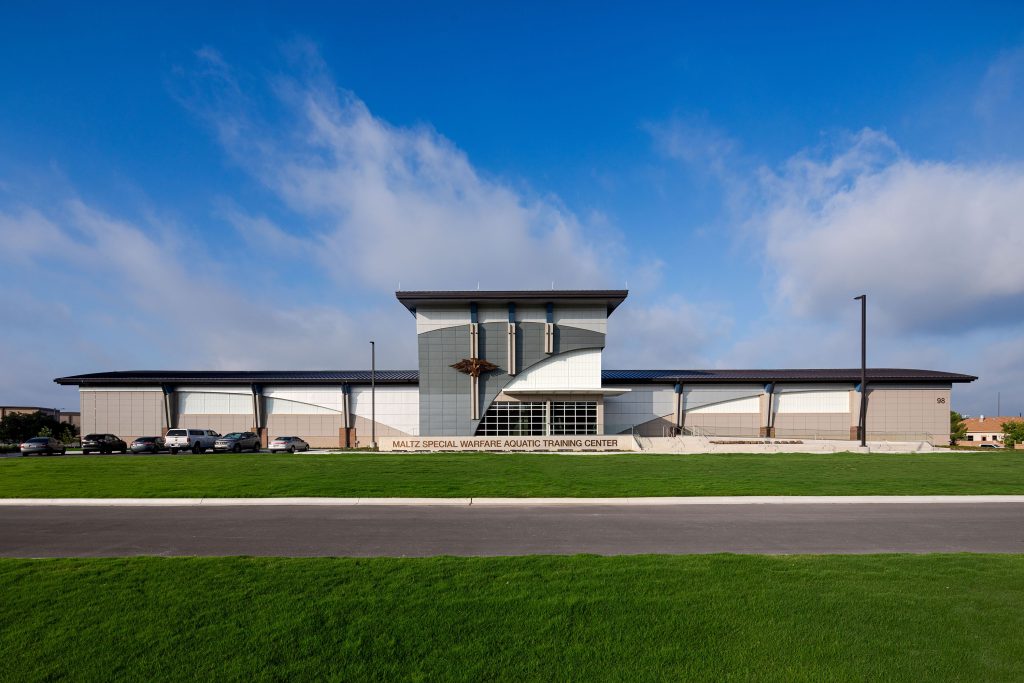
The special warfare training that occurs at Joint Base San Antonio, Texas, supports the growth and preparation of some of the most elite warriors in the U.S. Air Force in their mission to defend the United States and its interests. Today’s trainees are tomorrow’s warriors. These airmen require unequaled skills in search and rescue, pararescue, infiltration, exfiltration, and other action missions. Access to specialized training environments is crucial to ensuring the trainees receive the experience and instruction they need to prepare for future missions.
Previously, special warfare trainees at Joint Base San Antonio were using an outdated community pool built in 1969 that was inadequate for their rigorous requirements. Its limited depth, outdated mechanical systems, and frequent breakdowns led to canceled classes and a shortfall in certified trainees. This inadequacy necessitated the short-term use of an additional off-base community pool, which prompted privacy concerns and logistical challenges.
The existing security concerns, pool limitations, and inability to accommodate simultaneous classes at capacity challenged the base’s ability to effectively train recruits. The idea of developing an aquatic center to support special warfare trainees was born out of necessity to address training development needs and overcome existing limitations.
A Vision Realized
From a vision initially conceived in 2010 to a state-of-the-art facility completed in early 2024, the Maltz Special Warfare Aquatic Training Center, named in honor of Master Sgt. Michael Maltz, USAF, a pararescueman who heroically gave his life in 2003, is a testament to collaboration, technical excellence, and dedication to supporting the nation’s elite warriors.
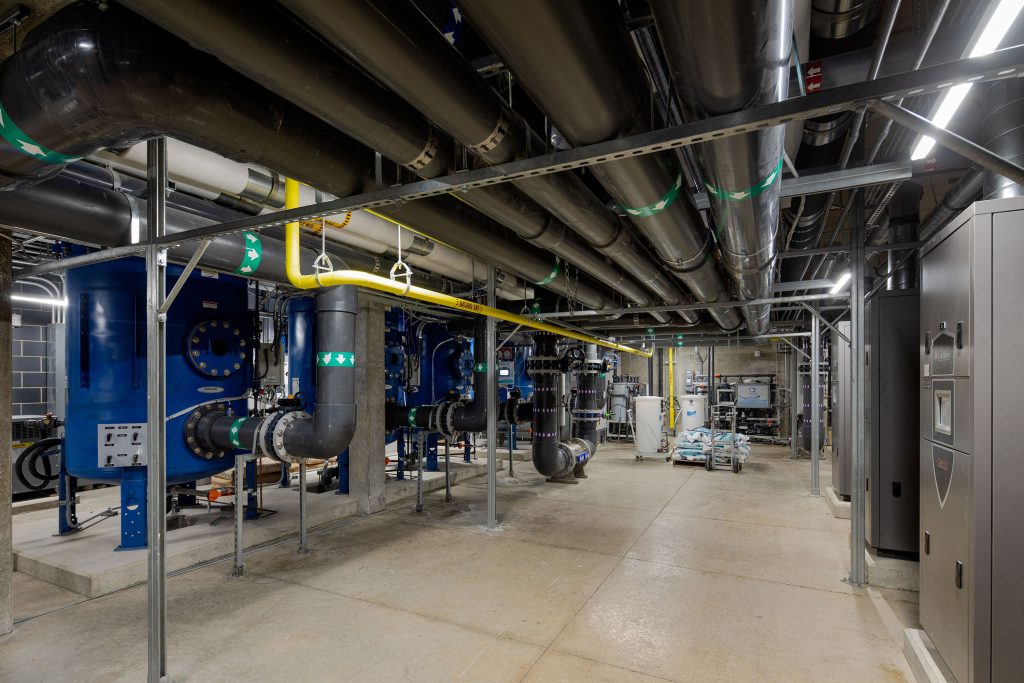
Multi-Agency Team. As the aquatic center project got underway, a team of experts was gathered to make the new training center a reality, representing a number of agencies, including the Air Force Civil Engineer Center, 802nd Civil Engineer Squadron, Special Warfare Training Support Squadron, and the Fort Worth District of the U.S. Army Corps of Engineers (USACE), as well as the Designer of Record, Tetra Tech, and joint-venture construction team, Clark-Byrne.
The new facility is purpose-built for special warfare trainees and is designed to withstand the rigorous rotating training programs. The two-story structure covers more than 76,000-ft², which makes it among the Air Force’s largest complexes. It includes two enclosed, climate-controlled 50-m pools of varying depths. These pools are separated by a central spine containing classrooms, medical spaces, locker rooms, and a human performance center.
The two-story structure covers more than 76,000-ft2, which makes it among the Air Force’s largest complexes. It includes two enclosed, climate-controlled 50-m pools of varying depths. These pools are separated by a central spine containing classrooms, medical spaces, locker rooms, and a human performance center.
Real-World Preparation. Designed to serve the unique demands of special warfare training, the facility is equipped to simulate real-life situations that trainees may encounter during search and rescue operations, infiltration, and other critical missions. The natatorium features specialized lane lines, a 15-ft catwalk, lane timers, underwater tie-offs, and a moveable bulkhead to adjust the pool’s dynamics. The pools also are equipped with an advanced filtration system capable of handling battlefield contaminants. As trainees jump into the pools and the water overflows to the sidewalks, the filtration system drains the water away, filters it, and reuses it, ensuring the water remains safe and clean for continued training.
Aesthetically, the facility is decorated with murals of warfighters in action and uses stainless steel ductwork. Each pool has four overhead circulating fans to aid in temperature control.
Collaborative Success
Through collaboration and trust, an open channel of communication allowed for rapid problem-solving and made sure that issues were addressed in real time, significantly expediting the project.
At the project’s start, it quickly became evident that traditional methods of addressing issues through Requests for Information would prove inadequate for the overall complexity of the work. Since many of the facility’s systems were uniquely designed for this project, there were often no standard answers to questions arising in the field. The solution came in the form of a Construction Services Agreement, which facilitated open lines of communication between USACE, the design team, and the construction contractor.
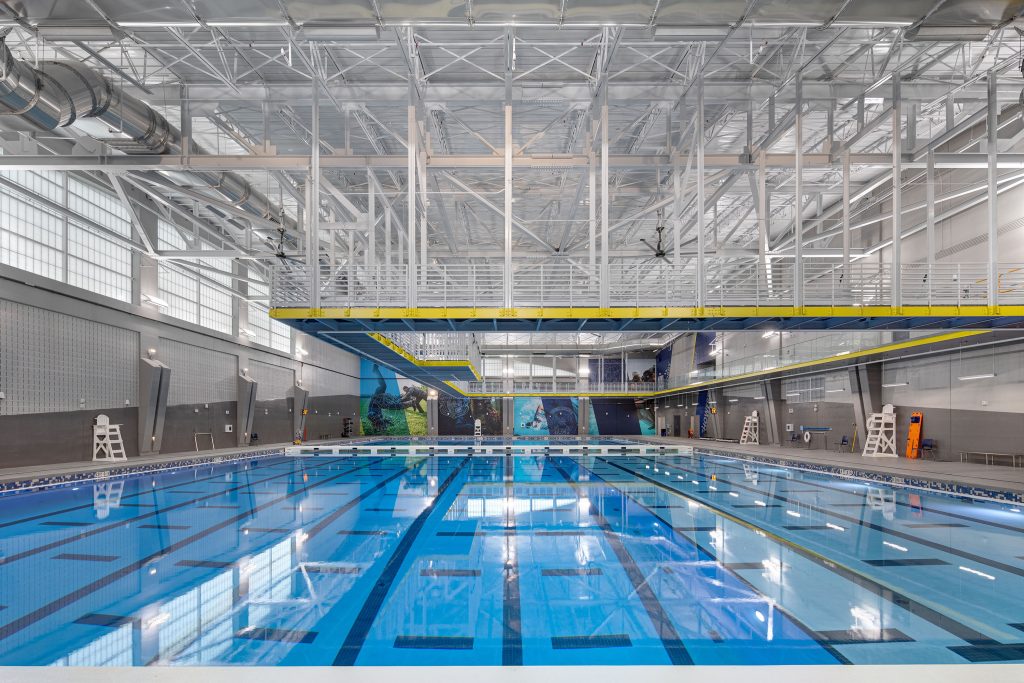
Weekly meetings and continuous communication facilitated quick resolutions to challenges. This kept the project on time and within budget. Every week, USACE Fort Worth District, the Designer of Record, the contractor, and subject matter experts would meet to discuss the facility’s status. They would work to overcome any challenges, expedite the problem-solving process, and significantly enhance project execution.
The project success is a testament to the efficiency of a cooperative and collaborative relationship between industry and government partners.
Technical Challenges
The size, technical complexity, and unique needs of this aquatic center presented several technical challenges for the design and construction teams. Addressing these and delivering the facility successfully required seamless coordination and innovation between stakeholders.
The facility’s structural steel trusses, each spanning 120-ft, relied on blind crane installation. Their massive size meant they had to be transported in two components and assembled on-site. Precise development and placement of truss pockets in the concrete walls were critical, as issues with fit would result in costly revisions. Careful collaboration between the installers, designers, and structural engineers successfully ensured the structural pieces fit seamlessly into the truss pockets despite demanding erection tolerances.
Another significant challenge was the foundation design, which needed to support the immense weight of the pools. The area selected for the facility’s construction was known to have expansive soils and posed a risk of heaving, which could compromise the facility’s integrity. The team was challenged to mitigate risk from both the soil’s uplift potential and the soil’s low bearing capacity in order to ensure that fluctuations in moisture could not threaten the pool’s integrity in differential settlements. Extensive engineering, including heavily reinforced concrete beams, ensured that the foundation could withstand these conditions. Careful coordination between teams was necessary in areas where the extensive subgrade mechanical systems interfered with the reinforced beam locations to ensure the pool’s hygienic operation.
The seamless integration of multiple systems, including filtration, chlorination, HVAC, and electrical conduits, posed further complications and required planning and adjustment through multi-discipline design coordination and logistics. Ensuring that all these systems were routed and functioning harmoniously was a challenge, but it was effectively overcome through the collaborative efforts between USACE Fort Worth District and the designer, contractor, and subject matter experts.
Serving Warfighters
The completion of the Maltz Special Warfare Aquatic Training Center demonstrates what can be achieved through stakeholder engagement, technical ingenuity, and a shared commitment to supporting our warfighters. From concept design to project execution, much thought and determination went into creating a facility tailored to improve the quality of life and readiness for current and future special warfare trainees.
The collaborative relationships, trust, and open communication from start to finish were pivotal in delivering this technically complex project on time and within budget. This success story underscores the immense benefits of trusted cooperation among stakeholders—transforming challenges into opportunities for innovation and excellence.
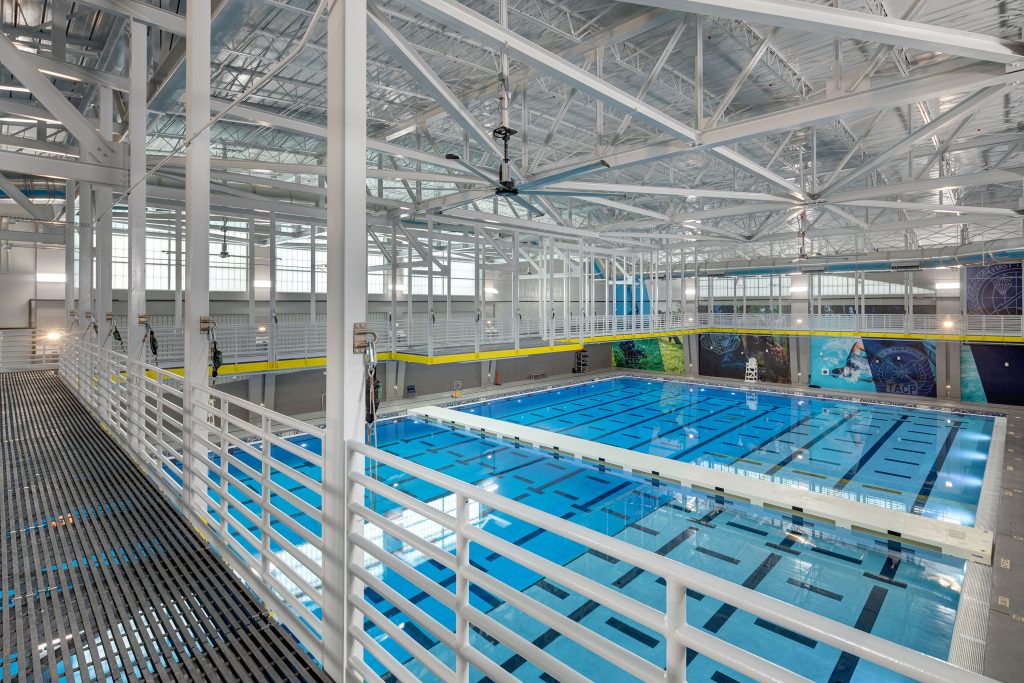
Bill Nieport, RA, PMP, LEED AP, M.SAME, is Vice President, Federal Operations, Tetra Tech; bill.nieport@tetratech.com
James Bush, P.E., M.SAME, is Project Executive, Clark Construction Group; james.bush@clarktexas.com
Daniel Olivas, P.E., PMP, is Resident Engineer, USACE Fort Worth District; daniel.c.olivas@usace.army.mil
Jerry Nicholson is Special Warfare Training Wing, Chief of Infrastructure, Joint Base San Antonio, Texas; jerry.nicholson@us.af.mil
Article published in The Military Engineer, November-December 2024
More News from TME
-
Leading the Way: Partnering for Resiliency and Readiness
TME Interview with Brig. Gen. Patrick Miller, P.E., F.SAME, USAF Commander, Air Force Civil Engineer Center -
Developing Tomorrow’s STEM Workforce Through Partnership
TME recently interviewed leaders of the Panama City Post about paying it forward, their repertoire of STEM outreach, and the benefits of collaborating with similar-minded professional organizations. -
Electrifying Solutions for Military Installations
As military installations implement electrification measures into the future, the challenges they face will not just require innovative technology solutions but embracing a holistic delivery approach implemented early in projects.