By Alison Lima, P.E., M.SAME, John Lee, PMP, M.SAME, and Col. Mike Geer, P.E., PMP, M.SAME, USAF (Ret.)
Establishing a physical presence in Korea and collaborating with local contractors can assist U.S.-based firms in successfully delivering federal projects on the peninsula.
Since 1957, the Far East District of the U.S. Army Corps of Engineers (USACE) has supported the mission of America’s military in the Pacific. Originally created to support the Army in Korea, the district’s program has expanded to serve the U.S. Air Force, U.S. Space Force, U.S. Navy, and U.S. Marines Corps by managing the design, renovation, construction, and maintenance of their facilities.
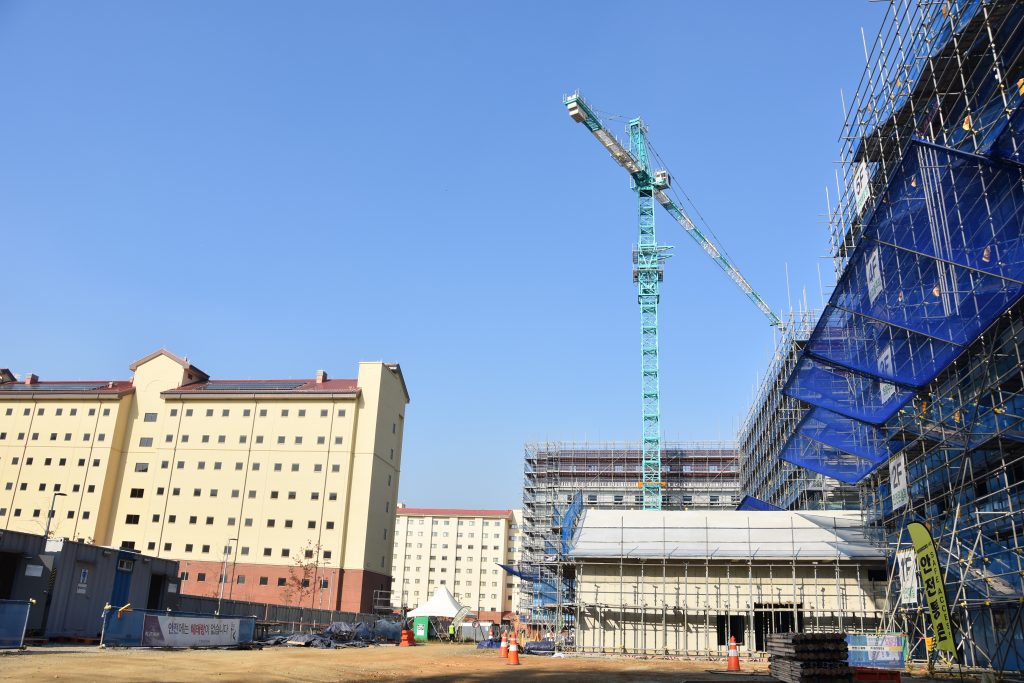
While many Far East District projects serve the military’s operational mission, countless others ensure the comfort and stability of servicemembers stationed in Korea. Tackling this initiative overseas comes with challenges, but by applying lessons learned and remaining committed to continuous improvement, design teams can resolve issues and meet project objectives.
As installations for both the United States and Korea are modernized through renovation projects and new facilities are added, U.S.-based contractors are learning the best delivery methods. With a large variation across time zones, technical requirements, and availability of local materials, American companies new to the region need to understand that common issues may be resolved in different ways. The processes they have used domestically or in other regions may not be as successful on the peninsula.
Leveraging Local Presence
In 2004, the Yongsan Relocation Program and Land Partnership Plan were authorized to relocate American forces to Army Garrison Humphreys. This $10.4 billion investment made Camp Humphreys the largest military installation outside of the United States as well as the new headquarters of the Far East District. In recent years, funding has been directed to further build out the base, including new family housing, schools, churches, entertainment centers, and other related facilities.
Along with Camp Humphreys, there are several other American bases in Korea as well as Republic of Korea Air Force bases that utilize the Far East District’s design and construction program. These installations, and their critical missions, are supported through various design initiatives—from the demilitarized zone down to the southern coast.
When working on water treatment plants, for example, certain components are not available at all within the country and require shipment from the United States.
When working with other international USACE districts, design firms often manage these projects out of their existing offices in the United States. Although this creates a solid foundation to work off, it is not a sustainable long-term model, especially considering the cost of travel. To mitigate these factors for projects located on the Korean peninsula, firms began to partner with Korean companies that could readily conduct site visits or meet in person with clients. As the workload increased, U.S.-based firms also began to hire local staff and form in-country offices to allow them to better serve their clients in the Far East District.
While there is still some management of teams across multiple time zones, local staff can much more easily attend site visits, check in with a client, or follow up on a construction project to answer Requests for Information. Having someone in country who understands issues on the ground and their relationship with the government is invaluable. It allows firms to build on their connections within the local architecture, engineering, and construction industries.
As staff shift between roles and locations on the client side, it is key that contractors provide consistency on their teams. There is no substitute for having that stable, local presence to ensure the quality of each project, understand each client’s needs, and properly pursue and price incoming work.
Differing Requirements
Designing military projects in Korea comes with unique challenges. Finding materials that are locally available and meet the Defense Department’s specifications can be difficult. When working on water treatment plants, for example, certain components are not available at all within the country and require shipment from the United States. Similarly, when designing a building with an elevator, there are limited manufacturers in Korea that meet those requirements. Cost estimators must keep track of which items are offshore and build in the associated shipping costs for each project.
When working on projects for the Far East District, designers need to consider the requirements for specific equipment that has been approved, such as whether they will utilize 110-V versus 220-V power plugs, to ensure it can function properly. Designers also need to think about the ease of upkeep. Although American servicemembers inhabit a lot of these facilities, Korean personnel conduct most of the operations and maintenance.
Humidity control is another critical design factor, given the geography of the country surrounded by ocean on three sides. Conditioning stairwells and equipment storage within military facilities has proven to be necessary, as condensation can lead to many problems. Understanding the local environment in which these buildings are located is vital.
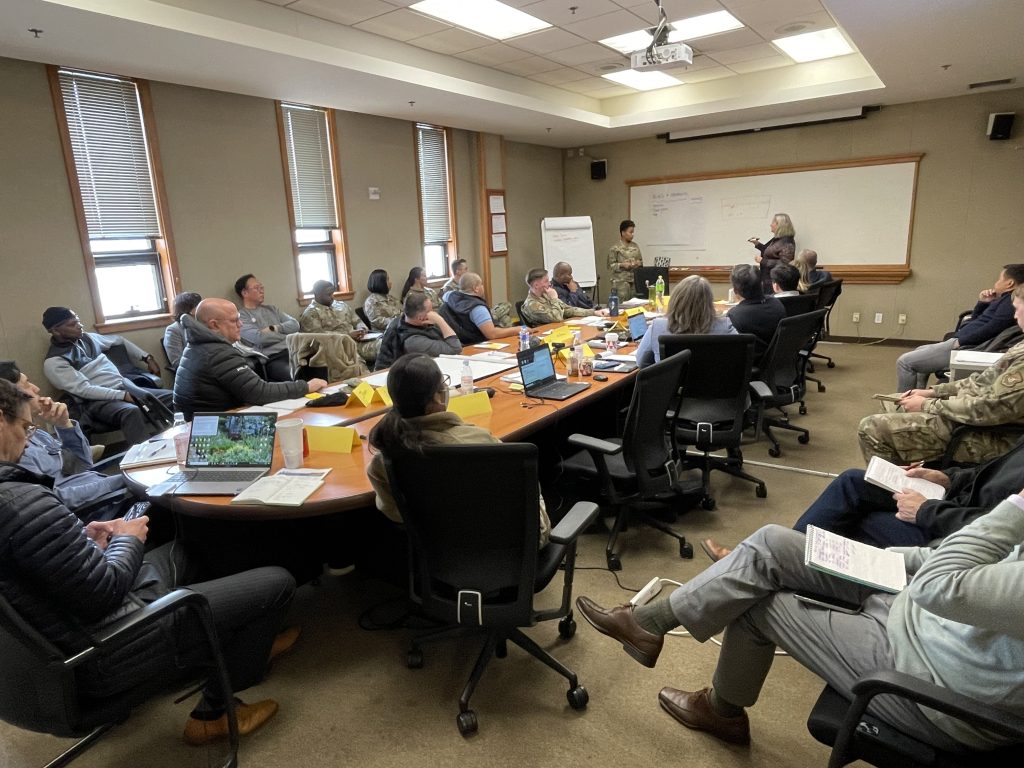
Because plans and specifications are printed and hand delivered to the Far East District, firms need to approach them with a different mindset. The design timeline may be tighter than expected, since final sets must be completed a few days before the deadline to allow time for printing, binding, and delivery. Design firms essentially have an added stage of quality checks to make sure that their submittals are ready to be printed on deadline.
Ensuring Quality
Once the 100 percent designs are completed, they are turned over to Korean construction contractors to build. Due to the differences in the design/construction industry between the two countries, it can be challenging for American design teams to determine all the details needed for Korean construction contractors. Experienced designers, however, have overcome the learning curve by providing a greater level of detail than what may be used on projects at installations in other regions of the world. By developing an understanding of construction contractor requirements, designers can do their part to ensure project success.
Preferred methods of construction are a crucial consideration for design teams. Contractors on the peninsula are most familiar with cast-in-place concrete for interior stairwells. Design teams conversely may prefer structural steel. To avoid problems with bidding, pricing, and scheduling, it is important to understand how the local construction contractors prefer to operate.
The contracting mechanisms for the Republic of Korea Funded Construction Program are typically Bill of Quantities or Bill of Materials. These require a different approach than U.S.-based contracts. By hiring local experts who understand this funding process, project delivery can be easier. Additionally, having staff who have native-level fluency in English and Korean as well as an understanding of both cultures also can help ease the process and allow firms to provide a more tailored approach.
Warfighter Support
Quality of life for American servicemembers in Korea is a top priority. While some may only spend a short time in the country, others spend years. The successful design and construction of temporary housing, dining facilities, fitness centers, and athletic fields is no small task.
The transformation of these installations into places of comfort, joy, and recuperation for members of our Armed Forces and their families allows firms to make a big impact in a rapidly growing area of the nation’s military operations.
Facilitating Teamwork
The SAME Korea Post has held multiple meetings over the past two years intended to bring together local construction contractors, U.S.-based design firms, the Far East District, and the Korean Ministry of Defense. This has allowed discussions in an open setting where attendees have been able to learn from each other and, uniquely, from members of the host nation’s defense sector.
Inviting these different organizations to convene helps increase partnerships between them, ensuring that each party feels confident in the funding that is being provided as well as encouraging a sense of belonging. This is especially important considering that the Far East District previously housed architectural-engineering services within its buildings for several decades as an extension of what the agency provided.
The overall increase in foreign, U.S.-based personnel who are working on these projects creates a learning curve on the client side as well. Understanding how things have been done in the past has become key to the successful completion of these projects, as both contractors and USACE move forward together in support of these overseas requirements.
Alison Lima, P.E., M.SAME, is Vice President, Global Services, John Lee, PMP, M.SAME, is Senior Project Manager, and Col. Mike Geer, P.E., PMP, M.SAME, USAF (Ret.), is Vice President, Global Services, Tetra Tech. They can be reached at alison.lima@tetratech.com; john.lee3@tetratech.com; and mike.geer@tetratech.com.
The opinions expressed in this article are those of the authors own and do not reflect the view of the Department of Defense, the Department of the Army, or the United States government.
More News from TME
-
Electrifying Solutions for Military Installations
As military installations implement electrification measures into the future, the challenges they face will not just require innovative technology solutions but embracing a holistic delivery approach implemented early in projects. -
Providing Benefits Through Adaptive Reuse of Federal Assets
Reconfiguring existing sites or buildings for a new mission has many inherent advantages to solve challenges that face federal entities, but key considerations need to be accounted for in order to maximize value. -
Driving Resilience Decisions Through Better Data
The Air Force Office of Energy Assurance is demonstrating how a new iteration of resilience assessments can better target and quantify potential vulnerabilities in energy security—bolstering national defense by supporting more informed decisions on resilience improvements at installations.