By Maj. Travis Vaughn, ANG, and Kyle Scoble
At McGhee Tyson ANGB in Knoxville, Tenn., the principal operation is in-flight refueling to enable extending the flying range of aircraft with the capability of transporting cargo, personnel, and medevac operations. The base also supports command and control, combat communications, and individual training. Primary units are the 134th Air Refueling Wing and 119th Command and Control Squadron. Additional tenants include the Air National Guard Training & Education Center, Air National Guard Band of the South, and an aviation support facility for the Tennessee Army National Guard.
In order to meet the modern needs of its aircraft maintenance operations and better support flying missions, the base recently completed its largest construction project ever—and a first step toward upgrading facilities to accommodate larger, newer aircraft: the KC-135 Maintenance Hangar and Shops.
The 57,400-ft2, LEED Silver hangar, which augments two other hangars on base built in the early 1950s, houses maintenance and corrosion control for the KC-135 Stratotanker refueling aircraft, and also has the capability to sustain the KC-46 Pegasus refueling aircraft. In addition, the hangar upgrades provide more than 20,000-ft2 of space for maintenance personnel working across multiple shops, including avionics, which utilizes a 100-ft-tall communication antenna to test and calibrate aircraft systems.
McGhee Tyson operates its mission with an important geographic centricity. Whether responding to homeland defense missions, providing routine training, or delivering Rapid Global Mobility, the base can deliver proximity to air refueling demands while remaining clear of the nation’s busiest airspace.
The new maintenance hangar will serve a key role in ensuring that airmen can continue to provide vital air mobility and air refueling capabilities in support of both Tennessee and the nation. But the path to reach that point was not without challenges.
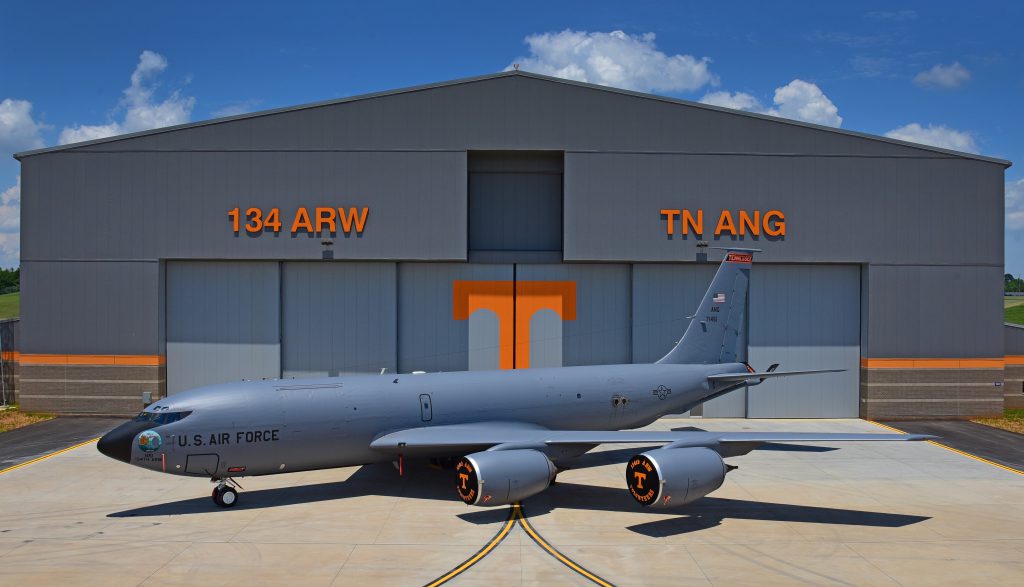
KC-46 Pegasus. PHOTO COURTESY MESSER CONSTRUCTION
PROACTIVE PLANNING
Alongside a newly constructed 10,000-ft runway, which was completed in 2021, the $32 million hangar project broke ground in fall 2019, with Messer Construction Co. leading construction and Burns & McDonnell serving as architect and engineer. Supporting hundreds of local jobs, including more than 100 subcontractor employees during the peak of construction, work also continued through the height of the COVID-19 pandemic, with minimal impacts to the workforce. Staying on track required the project team to adjust to early weather delays and overcome unexpected raw materials shortages. Proactive planning and a focus on safety and quality were crucial.
From a structural standpoint, the outside walls are 18-ft tall and slope up to 28-ft tall to match the hangar’s pitched roof. Inside, the flat ceilings are a maximum of 10-ft tall; this meant subcontractors were installing pipe and other systems 8-ft to 18-ft above those ceilings. Coordinating around such high up “dead” space was challenging and required significant logistical planning to ensure personnel (along with tools and materials) could get up and down safely without having to revisit the space on multiple occasions.
On the exterior, the steel structure reaches 80-ft high. The Tennessee Air National Guard elected to have a fall protection company install an engineered cable lifeline system for those working on or near the roof. It will remain permanently in place.
Another major effort involved the building envelope—specifically the challenge of minimizing energy loss to the shops section of the hangar. The air barrier is a combination of insulation, waterproofing, and caulking to eliminate water infiltration, reduce drafts, and regulate the loss of heating and air conditioning. Smoke testing was employed to ensure rooms were sealed off and contained.

IMAGE COURTESY MESSER CONSTRUCTION
ADDRESSING CHALLENGES
To aid in the coordination and layout of the hangar’s mechanical, electrical, and plumbing systems, the project team leveraged building information modeling. This allowed some of the ductwork and piping systems to be prefabricated and also revealed multiple clashes tied to imprecise light fixture heights and cable tray that needed to be designed around. These efforts resulted in minimal change orders.
Proactive, detailed planning. When installing mechanical, electrical, and plumbing, the top of the walls were braced with a series of kickers facing in alternating directions. This limited where duct and pipe could be placed. Avoiding the brace connections was an important component of successful installation, driven by proactive planning and a detailed quality plan.
The quality plan encompassed nearly 20 definable features of work utilizing an internal quality control system. Each definable feature began with a focused preparatory meeting that included all key personnel to ensure details, products, and expectations were discussed and known at the beginning. The team remained vigilant by performing more than 435 quality inspections throughout construction to remain accountable and reduce stress at the punchlist/turnover stage.
Focus on safety and quality. Throughout the project, it was ingrained in the team to stop work for safety and quality and to do what’s safe and what’s right. Deficiencies were caught along the way, such as the wrong data cabling being supplied to the site and switching it out for the specified and approved product prior to installation.
Additionally, a rebar placement issue was discovered during a pre-pour quality inspection that caused a one-day delay of a concrete pour. Still, this outcome was significantly better than having to remove a set section of concrete with a known deficiency later on, which would have impacted both time and cost.

focus on safety and quality.
MODERN CORNERSTONE
The 134th Air Refueling Wing celebrated the opening of the new hangar in June 2022. Once some final work on the flooring and fire suppression system is completed during the fall, the hangar will become fully operational.
With construction now complete, and the facility on its way to begin operations, this new hangar will serve as a major cornerstone in supporting the modernization of McGhee Tyson ANGB’s aircraft maintenance operations while allowing the base to serve its crucial role in the years to come.
Related Posts
-
Leading the Way: Partnering for Resiliency and Readiness
TME Interview with Brig. Gen. Patrick Miller, P.E., F.SAME, USAF Commander, Air Force Civil Engineer Center -
Developing Tomorrow’s STEM Workforce Through Partnership
TME recently interviewed leaders of the Panama City Post about paying it forward, their repertoire of STEM outreach, and the benefits of collaborating with similar-minded professional organizations. -
Electrifying Solutions for Military Installations
As military installations implement electrification measures into the future, the challenges they face will not just require innovative technology solutions but embracing a holistic delivery approach implemented early in projects.