By Brandt Takeuchi
As it develops cost estimates for military construction projects, Naval Facilities Engineering Systems Command utilizes a series of interrelated considerations, along with classification methodology, data resources, and software, to accurately navigate changing market conditions.
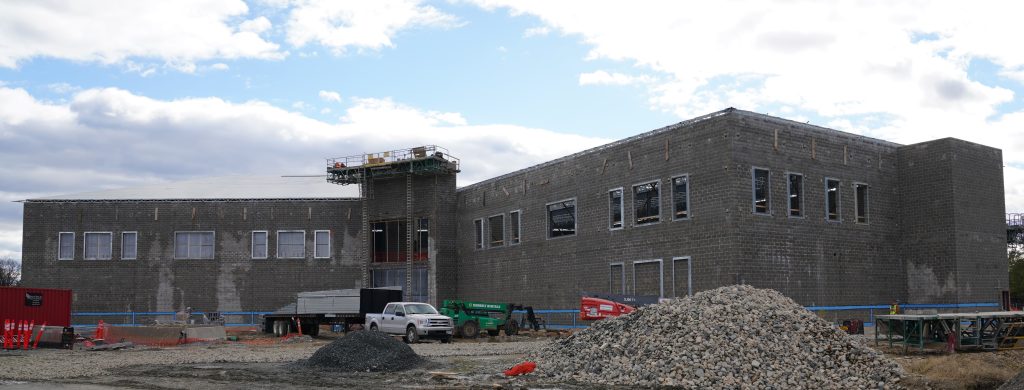
Cost estimating has always been a critical component in military construction (MILCON). The process is even more magnified as inflationary trends, schedule pressures, and material availability have grown more complex.
With a growing workload including record-breaking investments in support of shipyard optimization, Naval Facilities Engineering Systems Command (NAVFAC) continues to be challenged to develop and construct MILCON projects within these dynamic conditions. Factors such as supply and demand, labor constraints, and market competition play a significant role in cost development. But by committing to ongoing partnerships with A-E firms and construction partners, MILCON projects can more successfully be completed within budget, or more closely to the estimated costs.
There are four phases of cost development that NAVFAC follows for a MILCON project.
Developing Estimates
Defense Financial Management Regulations require budget requests for major construction to be supported by data on estimated costs. As projects progress through their lifecycle, Federal Acquisition Regulations require government cost estimates for each proposed contract. This pricing assessment supports federal acquisition strategies to deliver the best value product or service to the customer, while maintaining the public trust.
The criteria for preparing MILCON cost estimates are outlined in, specifically, UFC 3-701-01 DOD Facilities Pricing Guide; UFC 3-730-01 Programming Cost Estimates for Military Construction; UFC 3-740-05 Construction Cost Estimating; and Functional Criteria 1-300-09N Navy and Marine Corps Design Procedures. NAVFAC utilizes two cost estimating software applications to develop MILCON estimates. The MII v4.4.4 software supports full detailed quantity takeoff estimating; and the PACES 1.5 software supports parametric estimating.
In addition, resources to support cost estimate development include RSMeans, material pricing (vendor/supplier quotes), labor rates based on prevailing wages, and historical award data from comparable projects and primary facilities.
There are four phases of cost development that NAVFAC follows for a MILCON project.
- Planning/Programming Estimate: In this phase, preliminary scope requirements are developed, and cost estimates are often prepared based on historical data and comparable projects on a dollar-per-unit quantity basis. Higher contingencies are applied.
- Budget Estimate: Scope and requirements are further defined in this phase, with design development up to 35 percent. Cost estimates based on parametric costs have higher fidelity and lower contingencies.
- Design-to-Award Estimate: In this phase, scope and requirements are fixed. Designs are completed. Cost estimates are based on detailed unit costs and quantity takeoffs.
- Post-Award Contract Modification Estimate: This phase covers construction changes due to unforeseen conditions, customer-requested changes, and other schedule variables. Cost estimates are based on detailed unit costs and quantity takeoffs.
NAVFAC then classifies the estimates based on the Association for the Advancement of Cost Engineering Recommended Practice 56R-08, Cost Estimate Classification System. As stated in the guidance document, “the maturity level of project definition is the sole determining (primary) characteristic of class.”
The other characteristics are secondary, and they correlate to the maturity level of project deliverables.
Improving Delivery
It is important that estimate classification and project definition deliverables are aligned. In order to develop an accurate cost estimate, NAVFAC considers a series of related factors.
It is important that estimate classification and project definition deliverables are aligned. In order to develop an accurate cost estimate, NAVFAC considers a series of related factors.
- Market: Consider how the construction sector will look at the project. Elements of interest to bidders include project complexity, difficulty in accessing the worksite, who owns the risk (contractor or government), acquisition strategy, phasing plans, and subcontracting.
- Pricing: Obtain current material, equipment, and labor pricing. Localize estimate to the greatest extent possible.
- Labor: Determine labor availability (skilled trades, remote locations) by using prevailing labor rates for the specific location. Where is labor coming from? Is per diem required for housing? How are contractors attracting labor?
- Competition: Gauge the level of competition in the area.
- Risk Management: Utilize a Cost Schedule Risk Analysis to identify and mitigate risk early on.
- Escalation: Escalate project cost to the mid-point of construction using the recent NAVFAC Building Cost Index.
Budgetary Control
Cost estimating in the federal government often does not match the lowest bidder’s proposal. Instead, it aims to represent a fair and reasonable cost of a prudent, well-equipped contractor.
Each cost estimate is developed as accurately as possible, in as much detail as can be assumed, and based on the best information available. This holistic approach needs to be maintained throughout the entire project lifecycle.
Through stronger partnerships with industry, cost estimating does continue to improve. The more that it does will create greater budgetary control and improved performance for the critical missions these projects support.
# | Primary Characteristic | Secondary Characteristic | ||
Estimate Class | Maturity Level of Project Definition Deliverables Expressed as percent of complete definition | End Usage Typical purpose of estimate | Methodology Typical estimating method | Expected Accuracy Range Typical variation in low and high ranges at an 80% confidence interval |
Class 5 | 0% to 2% | Functional area, or concept screening | Square foot or square meter factoring, parametric models, judgment, or analogy | L: -20% to -30% H: +30% to +50% |
Class 4 | 1% to 15% | Schematic design or concept study | Parametric models, assembly driven models | L: -10% to -20% H: +20% to +30% |
Class 3 | 10% to 40% | Design development, budget authorization, feasibility | Semi-detailed unit costs with assembly level line items | L: -5% to -15% H: +10% to +20% |
Class 2 | 30% to 75% | Control or bid/tender, semi-detailed | Detailed unit cost with forced detailed take-off | L: -5% to -10% H: +5% to +15% |
Class 1 | 65% to 100% | Check estimate or pre bid/tender, change order | Detailed unit cost with detailed take-off | L: -3% to -5% H: +3% to +10% |
Brandt Takeuchi is Deputy Warrant Holder for Cost Engineering, NAVFAC Pacific; brandt.l.takeuchi.civ@us.navy.mil.
Article published in The Military Engineer, July-August 2024
More News from TME
-
Leading the Way: Partnering for Resiliency and Readiness
TME Interview with Brig. Gen. Patrick Miller, P.E., F.SAME, USAF Commander, Air Force Civil Engineer Center -
Developing Tomorrow’s STEM Workforce Through Partnership
TME recently interviewed leaders of the Panama City Post about paying it forward, their repertoire of STEM outreach, and the benefits of collaborating with similar-minded professional organizations. -
Electrifying Solutions for Military Installations
As military installations implement electrification measures into the future, the challenges they face will not just require innovative technology solutions but embracing a holistic delivery approach implemented early in projects.