By Brian Young, Ph.D., and Lori Dillon, M.SAME
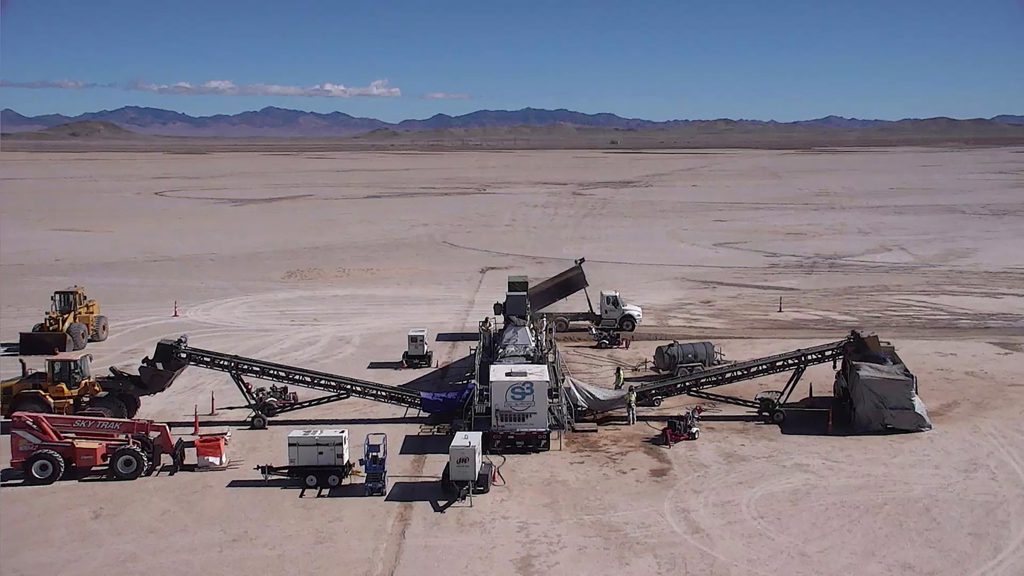
The largest cost for most remediation projects is waste transport and disposal. However, assuring that only contaminated materials undergo transport and disposal can help minimize these expenses. A recently developed waste reduction and soil sorting system, which has been in use at select defense sites for a couple of years, aims to screen and sort soils based on the presence or absence of radiological, elemental, volatile organic, or chemical signatures. These include dredge spoils; mining, oil, and gas wastes; and building debris and other bulk materials.
Based on current usage, the system has reduced the volume of site soils by approximately 90 to 95 percent, with only 5 to 10 percent of the original volume requiring off-site transport and disposal. Not only has this resulted in significant cost savings, but it leads to short project schedules—allowing for quicker cleanup and more sites to be remediated.
SCANNING IN ACTION
In designing the soil sorting system, a key consideration was flexibility to process a variety of wastes and identify multiple contaminants. Initial efforts focused on assuring the system would be able to survey 100 percent of the material that passed under the detection arrays, regardless of the contaminant.
Screening substances. Before entering the system, soil or other bulk material is passed through a screen to remove large items such as concrete and rebar that would not easily fit under the sensor array. Material is then loaded, typically by stacker conveyor, into a surge bin, after which it flows out and is distributed evenly at a pre-determined depth across the six-foot-wide main conveyor. This is accomplished by a screed, or “snowplow,” which is located between the surge bin and the sensor array. For typical operation, the material is spread roughly 58-in to 60-in wide and 2-in to 3-in deep, with a belt speed of 6-in/sec. The resulting throughput is roughly 60-yd3/hour to as much as 80-yd³/hour.
After being distributed by the screed, soil passes under the sensor array. This array is predetermined to meet the contaminant detection need of the project and is mounted before mobilization.
In order to address the vast range of contaminants of concern facing the environmental remediation field, an assortment of detection arrays were developed. For example, when used for radiological contamination, the system uses an array of large volume sodium iodide radiation detectors. Additional sensory arrays are able to sort of volatile organics, elementals such as mercury, and chemical contaminants.
Maximizing each array’s detection sensitivity to the contaminant is critical. The radiation detector array is housed within a lead shielding box, which prevents extraneous background radiation coming from the surrounding soil and environment, and maximizes sensitivity to radiation coming from material on the conveyor. The entire assembly (array and shielding box) is mounted on adjustable jack screws that can raise or lower the detector array. Typically, there is a gap of less than 1-in between the material and the detector array. This provides extremely close coupling for the sensors.
Leveraging automation. The digital output from the detector array is processed and analyzed second-by-second using onboard computer software. Results can be reported either as an activity concentration in the material (picocuries per gram) or as an absolute activity (microcuries). Then they are compared against
specified diversion threshold values that are set for the specific project. If the analyzed activity level is below the threshold, the material is considered “clean”; if the activity is above the threshold, the material is considered “hot” and triggers a diversion.
Diversion of material is handled by a second auto-reversing conveyor at the end of the main conveyor that runs perpendicular to it. Normally, the diversion conveyor runs so that when the material drops off the end of the main conveyor, it is caught and sent to the “clean” side. In typical operation, there is a third conveyor to catch the clean material and move it onto a managed pile or into awaiting dump truck. If a parcel of hot material triggers a diversion event, the controlling computer waits until that parcel of material drops off the end of the main conveyor and then runs the diversion conveyor toward the “hot” side, where the diverted material is caught by a container for later treatment and disposal actions.
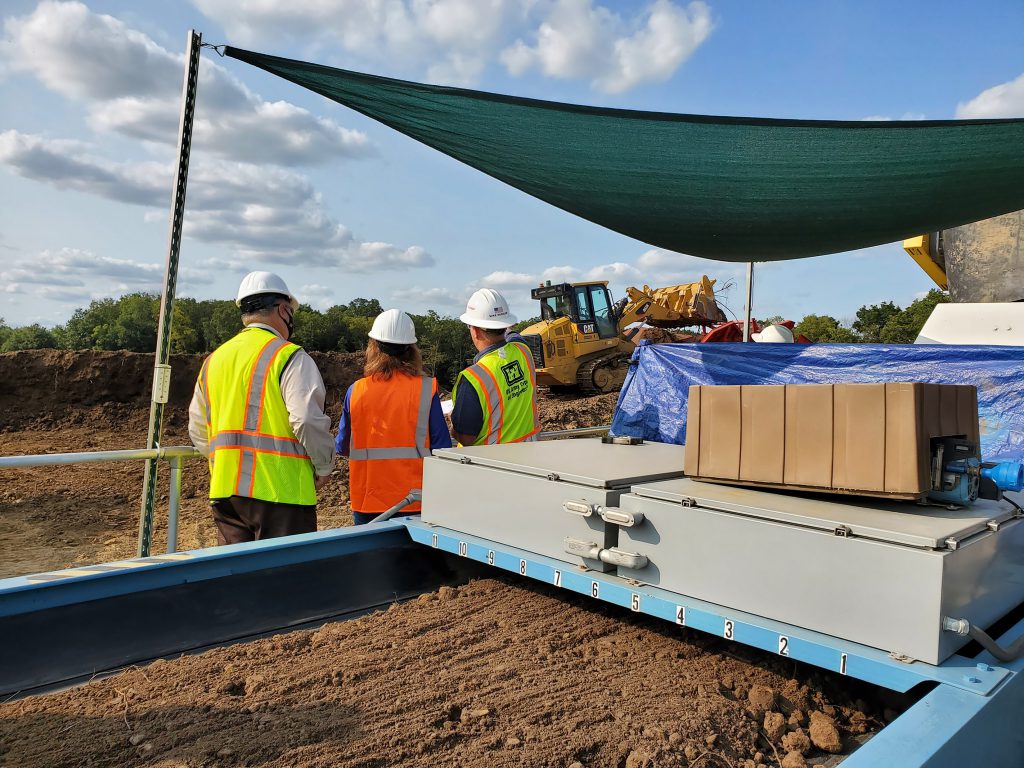
ADVANCING REMEDIATION
By uniformly spreading material, closely coupling material and detectors, and maximizing array detection sensitivity, soil sorting systems can reduce the volume of remediation bulk materials requiring waste transport and disposal. Along with the summary report of volume of material processed and diverted, the final data package includes any especially notable diversions or unexpected objects or nuclides identified. The package is backed up by the raw second-by-second data collected by the onboard computer.
By providing streamlined cleanup for a range of contaminants, soil sorting systems can be an effective tool at many remediation sites. In addition to reducing costs in waste transport and disposal, soil sorting systems also provide a savings on schedule duration, allowing a project to complete quicker and onto the next site.
PROVEN TECHNOLOGY
Soil sorting systems have been deployed to a number of remediation sites since their development. At the Iowa Army Ammunition Plant, a system has been deployed since 2019 to sort soil for depleted uranium. This site is active in the Formerly Utilized Sites Remedial Action Program, and the current deployment has had a total of 253 operational days with high operational availability. On this project, ISO-Pacific has sorted nearly 81,000-yd³ of material, of which only 13 percent was above criteria. Reducing the volume required for transport and disposal has significantly shortened the project timeline and saved millions in cost.
For the Middlesex Municipal Landfill Formerly Utilized Sites Remedial Action Program Site in New Jersey, ISO-Pacific worked with Ecology and Environment Inc. on a pilot study to establish the capability of the soil sorting system to effectively detect and isolate uranium ore nuggets present in fill material within the landfill. The work has delivered successful results to date.
More News from TME
-
Deploying Renewable Generation Through Small-Scale Hydropower
A field demonstration and ongoing investigation of modular hydrokinetic turbines by the U.S. Army Engineer Research & Development Center’s Construction Engineering Research Laboratory illustrates the potential applicability for using the technology on military deployments. -
Rethinking Traditional Treatment Systems for PFAS Remediation
At two U.S. Air Force bases impacted by historical releases of aqueous film-forming foam, innovative methods in treating PFAS in both surface water and groundwater provide examples of success in safeguarding health for military personnel and nearby communities. -
Tackling Restoration Projects With Amphibious Excavators
When faced with soft and wet underfoot conditions, such as at a recent channel dewatering, excavation, and repair project for USACE Galveston District, amphibious excavators offer a scalable way to contour difficult site characteristics.