By Dominique Gilbert, Sarah Grubisich, and Stephen Cosper, M.SAME
The U.S. Army Engineer Research & Development Center’s Construction Engineering Research Laboratory is working to develop small-scale waste-to-energy systems that will advance installation sustainability and waste management.
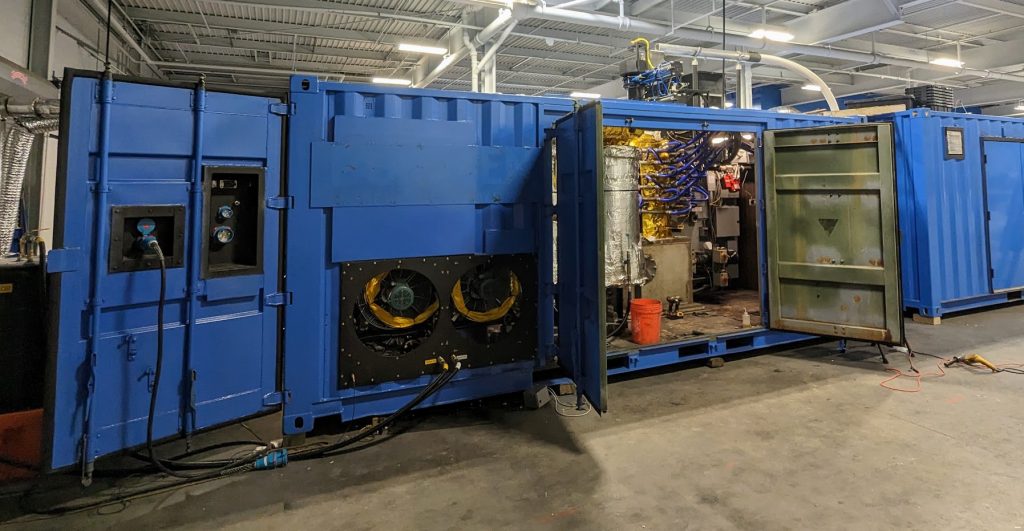
Photo courtesy ERDC-CERL
Adopting waste-to-energy solutions will be essential for the Department of Defense to meet sustainability objectives related to reducing waste and greenhouse gas emissions. By diverting waste from landfills, incinerators, and open burn pits, waste-to-energy significantly reduces the greenhouse gas emissions, toxic pollutants, and health risks associated with these more conventional disposal methods.
In addition to diverting waste from landfills and open burn pits, waste-to-energy offers another key benefit: the generation of resilient, secure energy. By producing energy from on-site waste, both fixed installations and operational environments can reduce dependence on external energy sources and improve resilience to energy disruptions and outages. This increased resilience is critical to ensure the effectiveness of mission-critical operations.
Influential Research
Over the past 10 years, the Construction Engineering Research Laboratory of the U.S. Army Engineer Research & Development Center (ERDC-CERL) has led upward of 15 research efforts targeting small-scale thermochemical waste-to-energy.
Current conventional waste-to-energy technologies employ either high-temperature thermochemical processes like pyrolysis, gasification, and combustion, or biochemical processes such as anaerobic digestion and fermentation.
Conversely, the small-scale waste-to-energy technologies being researched are innovative, forward-thinking waste disposal methods that are well-sized for the efficient waste management of military waste. They are cheaper and faster to implement than hauling waste offsite, and are safer than open pit burning, which has negative environmental effects and poses health risks to servicemembers and personnel working and living nearby.
Promising Technologies
Research conducted by ERDC-CERL on small-scale waste-to-energy systems have targeted a variety of potential technologies, including updraft and downdraft gasification, hydrothermal liquefaction, plasma arc, and pyrolysis.
All of these approaches employ high heat processes, ranging from hundreds to thousands of degrees centigrade, that convert the energy potential in the organic fraction of the waste (municipal solid waste, waste tires, hazardous waste, and food waste) into energy (syngas, electricity, and/or thermal).
Each method employs a different conversion-to-energy process.
Gasification. This technology comprises two varieties: downdraft and updraft. Downdraft gasification generates an energy product that is low in tar. The waste feedstock usually requires a homogenization step, then it is fed into the reactor from the top while the air is fed downward into the system. The waste feedstock is converted into a relatively clean, low tar combustible syngas (mainly carbon monoxide and hydrogen) suitable for use in a spark internal combustion engine.
In comparison, updraft gasification systems tend to be simpler in design and have higher thermal efficiencies than downdraft systems. The waste feedstock is fed into the reactor from the top while the air is fed into the reactor from the bottom. This process can create a syngas that is high in molecular weight (in the range of commercial petroleum products), which gives it a high heating value. This syngas may contain heavy tars, but with some simple clean-up steps can be introduced into a diesel engine (such as a 60-kW AMMPS generator or microturbine) to create electricity.
Hydrothermal Liquefaction. A system with hydrothermal liquefaction is used to process wet organic feedstocks like sewage sludge, food waste, and algae. It uses water under high temperatures and pressure (up to 370°-C and 3000-psi) to depolymerize the feedstock.
The high pressure keeps the water in liquid form, while some of the heat energy is recovered to make the process less energy intensive. Hydrothermal liquefaction converts organics into bio-crude oil or fuel, which can be refined into commercial fuels.
Plasma Arc. This process uses a plasma torch/arc and can produce syngas from organic materials. A plasma arc employs a high-current, low-voltage electrical discharge between electrodes that is created by passing an electric current through a gas, such as argon or nitrogen. The main attraction of plasma arc systems is that they can mineralize almost any substance, albeit at a relatively high energy cost.
Pyrolysis. This technology is essentially an oxygen-free endothermic, externally heated process operating at low pressure. These systems tend to be the most environmentally benign waste-to-energy approach. Some pyrolysis systems can destroy toxic compounds (like polycyclic aromatic hydrocarbon and polychlorinated biphenyls) and can convert halogens, if present in the feedstock, to simple salts. In some systems, toxic dioxins or furans are eliminated. The syngas created through pyrolysis can be used in gas turbines and internal combustion engines.
Developing and Validating
Preliminary results from ERDC-CERL’s research are promising. The efforts are focused on developing and validating systems that meet four established criteria: they are environmentally benign; they can produce electricity; they can be proven economical with a wide selection of waste feedstock; and they can be containerized for easy delivery to operational environments.
Specific research considerations encompass factors such as system throughputs, waste types, feedstock compositions, emissions, performance consistency, ease of operation, and mobility.
Of the systems that have completed testing, two demonstrated the capability to process waste feedstock recipes that consisted of different proportions of mixed waste (wood, food, paper, old corrugated containers, textiles, plastics, steel, non-ferrous metal, glass, and sewage sludge), as well as the capability to process plastics waste processor disks (generated by the U.S. Navy).
Notably, all of the systems demonstrated the potential for a positive net present value or cost savings.
- Most of the systems under study are containerized. The system footprints vary (from one to five 20-ft shipping containers) depending on the intended feedstock throughput and whether feedstock pre-processing or power conversion requirements are engineered into the system design.
- Most of the systems under study demonstrated total compliance with Environmental Protection Agency gaseous emissions requirements. None of the systems exceeded federal limits for dioxins and furans.
- Some of the systems under examination can be used to generate clean electricity, and some use a portion of the energy they generate to sustain their own waste-to-energy conversion processes. In total, the systems generate different types of energy (syngas, electricity, and thermal).
Safe and Sustainable
The path forward for ERDC-CERL is to continue working with the technologies to develop small-scale waste-to-energy systems that meet the four criteria (environmentally benign; produce electricity; economical with multiple waste feedstock; and easily deliverable to operational environments). ERDC-CERL is currently engaged with the DOD Operational Energy Prototyping Fund, Army G-9 Installations, and the Assistant Secretary of the Army for Installations, Energy & Environment, to develop small-scale waste-to-energy innovations.
The overall vision is for small-scale waste-to-energy to facilitate pollution-free waste management at fixed installations, remote locations, and island nations. This technology could offer a safer and more sustainable alternative to landfilling and open burn pits while providing an additional resilient energy source.
Dominique Gilbert is Program Manager, Waste-to-Energy and Plastics Research, Sarah Grubisich is Sustainability Specialist, and Stephen Cosper, M.SAME, is Environmental Engineer, U.S. Army Engineer Research & Development Center – Construction Engineering Research Laboratory. They can be reached at dominique.s.gilbert@usace.army.mil; sarah.l.grubisich@usace.army.mil; and stephen.d.cosper@usace.army.mil.
More News from TME
-
Rethinking Traditional Treatment Systems for PFAS Remediation
At two U.S. Air Force bases impacted by historical releases of aqueous film-forming foam, innovative methods in treating PFAS in both surface water and groundwater provide examples of success in safeguarding health for military personnel and nearby communities. -
Eliminating PFAS Leaching at Camp Grayling
At Camp Grayling, a novel colloidal-activated carbon material was used as a horizontal barrier on a site where aqueous film-forming foam had previously been discharged to prevent PFAS from leaching into groundwater. -
Investigating Emerging PFAS Destruction Technologies
Following recent interim guidance from the Department of Defense on how military organizations are to handle the destruction and disposal of PFAS, developing technologies that target the destruction of these forever chemicals hold possibilities for effective and efficient removal.