By Lt. Cdr. Allison Pontal, P.E., M.SAME, CEC, USN
Hurricane Florence made landfall as a Category 1 storm on Sept. 14, 2018, 43-mi south of Marine Corps Base Camp Lejeune, N.C. Over the course of two days, Florence proceeded to drop record rainfall of more than 30-in. The storm also carried 100-mph wind gusts that caused significant damage to facilities, landscape, and infrastructure, including a number of U.S. Marine Corps installations.
The damage sustained to three bases across the region—Camp Lejeune, Marine Corps Air Station Cherry Point, and Marine Corps Air Station New River—required a substantial repair ($1.7 billion) and replacement ($1.7 billion) effort to restore readiness capabilities to full strength. As part of the overall program, contracted by Naval Facilities Engineering Systems Command (NAVFAC), a $192.7 million MILCON package was awarded in August 2020 to RQ-WM Jordan JV, which included the construction of the P1338 II Marine Expeditionary Force Simulation Training Replacement building. The 54,000-ft2 simulation training facility will contain the II Marine Expeditionary Force Battle Simulator Center and Combined Arms and Staff Trainer and will include multiple configurable simulation training classrooms, configurable First Integrated Rehearsal Environment classrooms, and outdoor training areas.
The project broke ground on June 7, 2021. In order to efficiently cast and place the facility’s walls, concrete tilt-up panel construction was employed over conventional masonry component construction. This method was chosen due to the cost savings associated with it, scaffolding safety consideration impacts when compared to conventional masonry walls, and the expedited completion of the facility’s exterior structure.
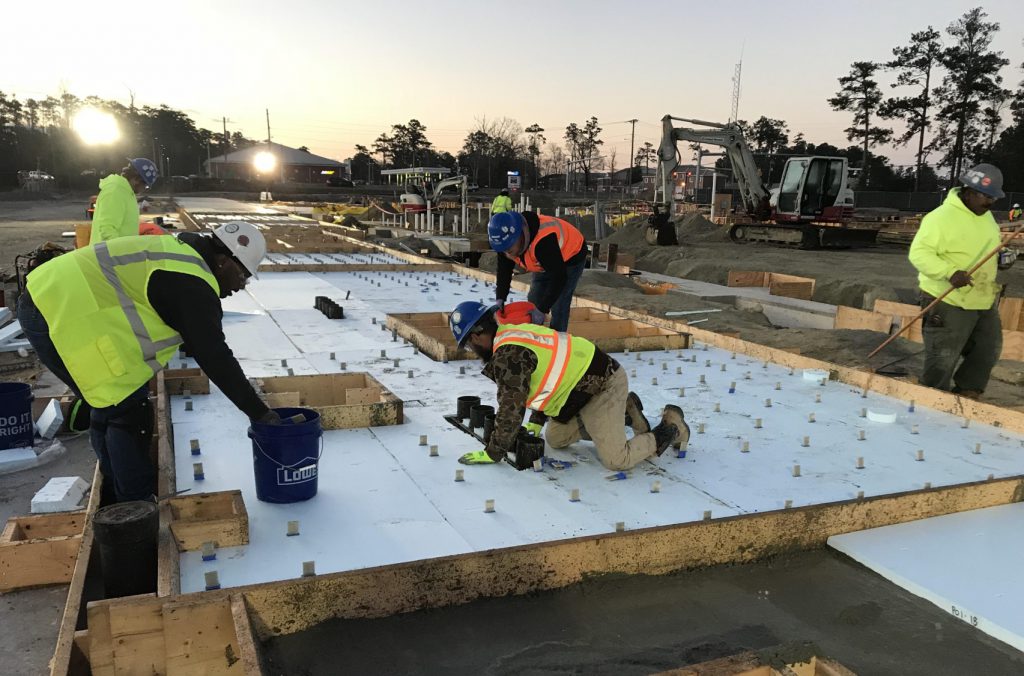
To expedite delivery of the P1338 II Marine Expeditionary Force simulation training replacement building at Marine Corps Base Camp Lejeune, tilt-up concrete panel methodology was employed. PHOTOS COURTESY OICC FLORENCE
DETAILED ENGINEERING
Construction required the creation of 56 individual concrete wall panels, which were all cast on site. Wooden frames were used to create the general form of the 30-ft long and 15-ft high wall. The 11-¼-in thick wall was composed of first a plastic liner that held the thin brick veneers, reinforcing steel, and initial utility conduit. Next, 6-in of concrete was placed, followed quickly by an insulation panel and the installation of 6-in Thermomass tabs that connect and tie the initial concrete layer and insulation layer to the final concrete layer.
Once proper cure time was achieved on the initial layer, and the connective fiberglass tabs were pull tested for adhesion, a second 6-in of concrete was placed over additional reinforcing steel. Finally, a smooth trowel finish was achieved.
Each panel was heavily engineered prior to any work being conducted on site. Multiple drawings for each of the 56 panels were drafted, and utility cut outs and door and window openings were reviewed by multiple trades to ensure compliance with specifications. The detailed panel engineering ahead of casting and concrete placement factored into the success of the quick erection of the facility. This also mitigated costly rework and schedule delays.
The initial 15 panels were formed, placed, and cured within three weeks of initiation. Completion of all 56 panels took just three months, utilizing 350-yd³ of concrete throughout the process overall. Once cured, the tilt-up placement of all 56 panels only took seven working days. Cost savings for the facility were estimated at roughly $18.79-psf (totaling $996,000).
In addition to time and cost savings, NAVFAC recognized the ability to quickly ensure quality craftsmanship as an important benefit to tilt-up construction during the casting portion of work. Minimizing hazards factored in with the elimination of scaffolding and excess masonry crews on site.
The durability and weather tightness of tilt-up construction also delivered several crucial long-term advantages, including increased insulation and reduced maintenance costs, lowering future mission impact.
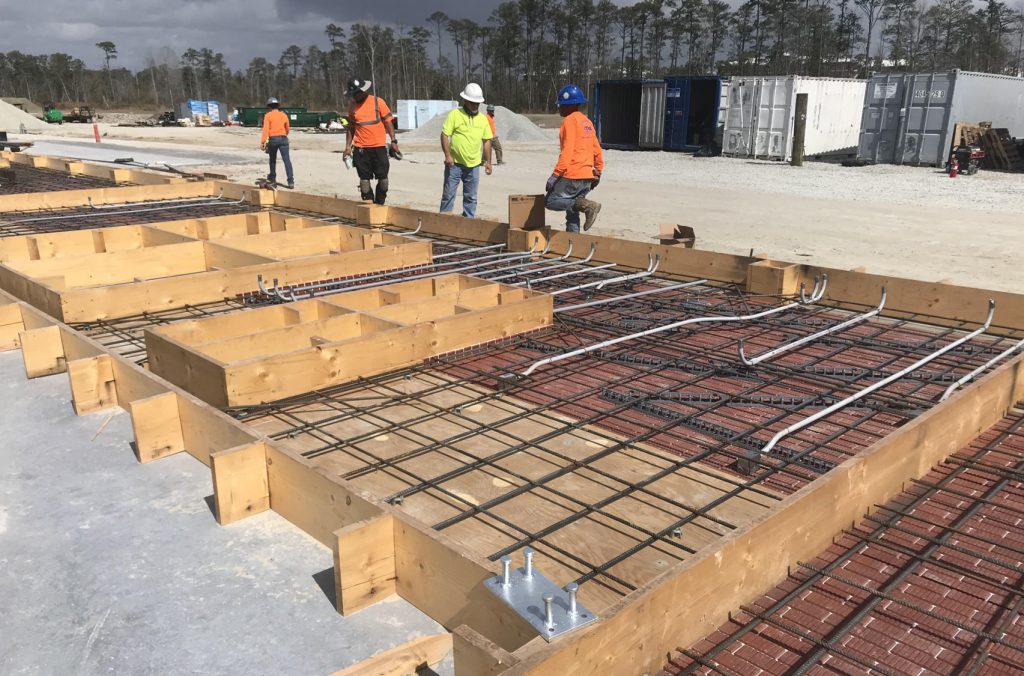
RETURNING TO OPERATIONS
With the approval of the tilt-up concrete wall panel methodology, the contractor was allowed maximum flexibility and innovation to rapidly meet mission requirements. Remarked Capt. James Brown, CEC, USN, Commanding Officer, Officer in Charge of Construction Florence: “The decision to use cast concrete panel construction on this project provides an excellent example of how creativity, ingenuity, and a willingness to depart from conventional construction methodologies can create increased value to both the government and the contractor.”
The simulation training facility at Camp Lejeune—scheduled for completion in spring 2023—and other modernized buildings and infrastructure across the region financed in the aftermath of Florence, will now better serve their mission to help prepare Marine Corps personnel for their mission.
Related Posts
-
Leading the Way: Partnering for Resiliency and Readiness
TME Interview with Brig. Gen. Patrick Miller, P.E., F.SAME, USAF Commander, Air Force Civil Engineer Center -
Developing Tomorrow’s STEM Workforce Through Partnership
TME recently interviewed leaders of the Panama City Post about paying it forward, their repertoire of STEM outreach, and the benefits of collaborating with similar-minded professional organizations. -
Electrifying Solutions for Military Installations
As military installations implement electrification measures into the future, the challenges they face will not just require innovative technology solutions but embracing a holistic delivery approach implemented early in projects.